PLB HDPE ducts, short for Permanently Lubricated High-Density Polyethylene ducts, are used in due
to their robust and durable nature. Also known as PLB HDPE Ducts, these products come with numerous benefits such
as flexibility, and high tensile strength, making them a preferred choice for many industries.
As India’s leading manufacturer & supplier of high-end engineering products, we offer high-quality PLB HDPE ducts made from virgin, UV-grade HDPE materials to ensure optimal performance for copper cable and optic fibre deployment. These products adhere to global and TEC standards, guaranteeing durability and reliability across various applications. The ducts consist of two concentric layers: the outer layer is HDPE, co-extruded with an inner layer of solid permanent lubricant (silicon) to reduce the internal coefficient of friction (ICF). This design increases resistance to mechanical and natural damage, thereby improving cable protection.
When considering PLB HDPEDucts options, one must also take into account the PLB HDPE Ducts price, which can vary based on the diameter, length, and additional features of the pipe. It's essential to compare the PLB HDPE Ducts price from different suppliers to ensure you get the best value for your investment.
We maintain a ready stock available at reasonable prices, ensuring fast delivery to meet urgent demands. The raw materials are sourced from major industry players, guaranteeing high quality. We have earned a stellar reputation in both government and private sectors for our reliable and efficient service. Our commitment to delivering exceptional quality has made us the top PLB HDPE Ducts manufacturer & supplier in India and abroad.
Utkarsh PLB HDPE Ducts are designed to minimise internal friction because of the innovative co-extrusion design that reduces the internal coefficient of friction (ICF). This feature helps lower the risk of friction-related damages and facilitates smooth cable installation, which makes our items ideal for telecom and infrastructure projects throughout Eastern India.
As India’s leading manufacturer & supplier of high-end engineering products, we offer high-quality PLB HDPE ducts made from virgin, UV-grade HDPE materials to ensure optimal performance for copper cable and optic fibre deployment. These products adhere to global and TEC standards, guaranteeing durability and reliability across various applications. The ducts consist of two concentric layers: the outer layer is HDPE, co-extruded with an inner layer of solid permanent lubricant (silicon) to reduce the internal coefficient of friction (ICF). This design increases resistance to mechanical and natural damage, thereby improving cable protection.
When considering PLB HDPEDucts options, one must also take into account the PLB HDPE Ducts price, which can vary based on the diameter, length, and additional features of the pipe. It's essential to compare the PLB HDPE Ducts price from different suppliers to ensure you get the best value for your investment.
We maintain a ready stock available at reasonable prices, ensuring fast delivery to meet urgent demands. The raw materials are sourced from major industry players, guaranteeing high quality. We have earned a stellar reputation in both government and private sectors for our reliable and efficient service. Our commitment to delivering exceptional quality has made us the top PLB HDPE Ducts manufacturer & supplier in India and abroad.
Utkarsh PLB HDPE Ducts are designed to minimise internal friction because of the innovative co-extrusion design that reduces the internal coefficient of friction (ICF). This feature helps lower the risk of friction-related damages and facilitates smooth cable installation, which makes our items ideal for telecom and infrastructure projects throughout Eastern India.
-
44000
Plant Area
-
68000
Production Capacity
-
5000
Ready Stock
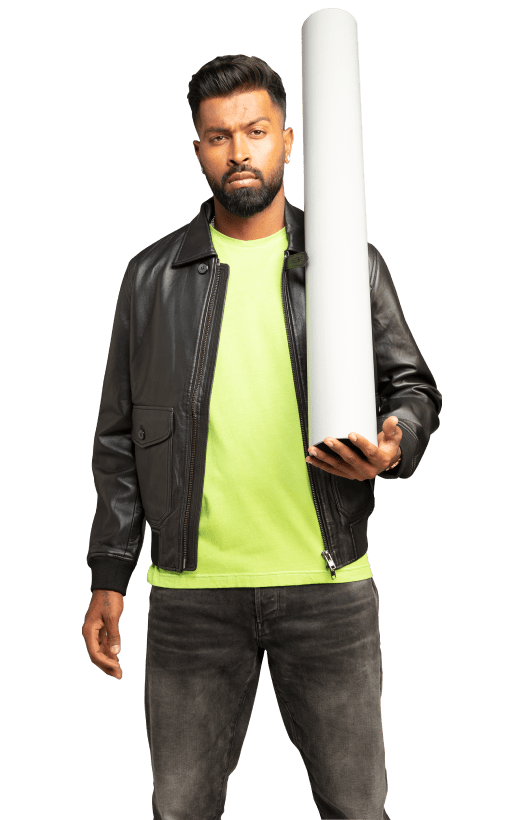
Product Specifications
Our PLB HDPE Duct pipes come with robust specifications, and are engineered for durability, safety and seamless performance in diverse applications.
Explore the technical properties of our PLB HDPE Duct pipes, featuring UV-certified materials and advanced design for superior performance.
- Manufactured as per TEC standards and specifications of TEC/GR/TX/CDS-008
- Available in sizes of 32/26 mm, 40/33 mm, and 50/42mm.
- Manufactured as per TEC standards and other international standards.
- Detailed product testing, including Reversion test, Melt flow rate (MFR) density, Overall Migration test, Carbon Black content, and Dispersion, Oxidation Induction test.
Comprehensive standards adhered to in our range of PLB HDPE Ducts, for assured quality and reliability.
- Virgin Grade, UV-Certified Materials
Crafted with virgin-grade, UV-certified raw materials, our PLB HDPE Ducts ensure unmatched quality and durability. The co-extruded inner lining with permanent solid lubricants (Silicon) guarantees smooth operation and extended lifespan. - Exceptional Damage Resistance
Designed to withstand the toughest conditions, PLB HDPE Ducts offer excellent resistance to both natural and mechanical damage. This robust construction makes them ideal for challenging environments. - Lightweight and Temperature-Resistant
Our PLB HDPE Ducts are not only lightweight, making them easy to handle, but also temperature-resistant, ensuring reliable performance across a wide range of applications. The low coefficient of friction further enhances their efficiency. - Available in 8 Vibrant Colours
Choose from 8 different colours (Green, Orange, Blue, Yellow, Brown, Violet, Grey & Red) to suit your project’s needs. Whether for identification or aesthetic purposes, the variety ensures flexibility and customisation - Environmental Stress Crack-Resistance
PLB HDPE Ducts are engineered for environmental stress crack-resistance, providing longevity and reliability in diverse conditions. Plus, they’re designed for easy future upgrades, offering flexibility for expanding projects. - Competitive PLB HDPE Ducts Price
All these premium features come with a competitive PLB HDPE Ducts price, ensuring you get the best value without compromising on quality or performance.
A snapshot of the distinct advantages of our PLB HDPE Ducts, engineered for durability, flexibility, and seamless installation in diverse applications.
- Lightweight and Flexible Design
PLB HDPE Ducts are known for their lightweight nature and enhanced flexibility, making them easy to transport and handle. These features contribute to reducing overall project costs, especially when considering the PLB HDPE Ducts price. - Easy and Efficient Cable Installation
The design of PLB HDPE Ducts allows for the easy and fast installation of Optic Fibre Cables (OFC) or Copper Cables, requiring less manpower. This efficiency not only saves time but also adds value when assessing the PLB HDPE Ducts price. - Non-Toxic and Convenient Handling
PLB HDPE Ducts are non-toxic and easy to handle, making them a safe choice for various applications. Available in coils, they offer convenience in storage and transportation, which is an essential factor when evaluating the PLB HDPE Ducts price. - Fewer Accessories Required
With a reduced need for additional accessories, PLB HDPE Ducts streamline installation processes. This simplicity is reflected in the overall cost-effectiveness, further enhancing the attractiveness of the PLB HDPE Ducts price. - Ideal for OFC Installation by Blowing/Pulling Method
PLB HDPE Ducts are perfectly suited for installing Optic Fibre Cables using the Blowing/Pulling method, ensuring a smooth and efficient operation. The versatility and reliability of these pipes justify the competitive PLB HDPE Ducts price.
Application Areas
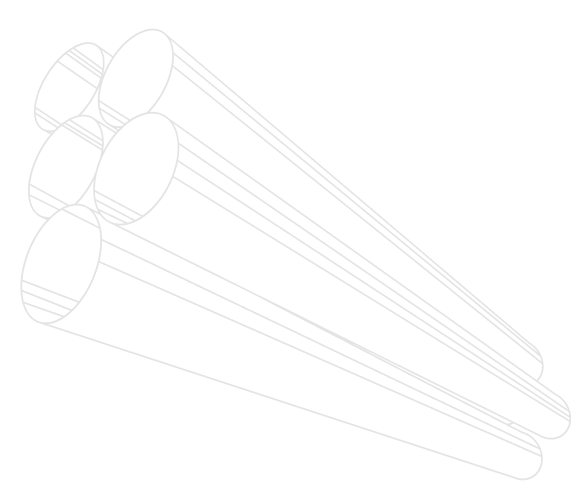
Manufacturing Process
A meticulous manufacturing process is followed for our range of PLB HDPE ducts, right from raw material selection through final inspection and packaging.
-
Raw Material Preparation
The raw materials and pigments are fed into a mixer via an automatic system, using a pre-set recipe. The preheated granules are then sent to the extruder hopper.
-
Material Feeding
Material is introduced into the extruder through a hopper and controlled by a gravimetric or volumetric system to ensure accurate feeding.
-
Melting and Mixing
Inside the extruder barrel, the material is heated to its melting point, around 200°C, through a combination of load (melt pressure) and friction in the screw system.
-
Pipe Formation
The melted material is pushed through a die-head (spider), where it is formed into a pipe shape.
-
Calibration and Cooling
The pipe is calibrated to the correct size in a vacuum sizing tank and then cooled with water in a spray tank.
-
Printing and Cutting
At the end of the production line, pipes are printed and cut into lengths or coiled based on their intended use.
-
Quality Control and Dispatch
Pipes undergo online inspection and testing by QC. Following post-activity checks and final inspection by QA, the pipes are dispatched as per the delivery order.